Remote Quality Control: A Superpower to Reduce Rework
The construction industry is one of the most resource-intense industries. In addition, ten percent of all materials are wasted due to rework. Digital tools, such as remote quality control, aim to make these reworks obsolete.
Author
Reconstruct Inc.
Reconstruct is a SaaS platform that utilizes images and videos from 360 cameras, drones, and cell phones to produce 3D reality models and automatically aligns these models over a project’s timeline.
This article belongs to the collection Quality & Efficiency
To the topic pageThere are 1,000 ways of miscommunicating on the progress and quality of a construction project. But it doesn't have to be this way: Remote quality control with reality mapping technology enables construction teams to easily and quickly map areas, elements, or work locations and visualize in 2D or 3D. With those realistic experiences of project sites, on-site and remote workers can review the work put in place and identify actual or potential quality issues before they snowball into real problems.
Construction and operations teams can produce 2D reality maps and 3D reality models from cell phones, drones, and 360° video cameras – resulting in measurable reality maps to the centimeter or even sub-centimeter resolution, on a daily or weekly basis. This reality mapping technology is a great addition to three-dimensional laser scanning (LIDAR), also much quicker and cheaper. It can catch many quality issues such as the positioning of conduit, embeds, openings as well as rebar spacing during concrete placement operators - before they have a major impact on project schedules and budget.
Map, Walk, and Measure Reality
Photogrammetry and videogrammetry technology, as for example Reconstruct Inc. offers, produces a 2D reality map and 3D reality model from camera-based reality capture. This level of detail in a digital site provides the ability to perform remote quality control. Construction teams benefit in a number of ways because the review work is put in place against the design works, no matter if those consist of 2D drawings or a BIM model. It is also possible to ensure the correct placement of embeds, openings, concrete sleeves, rebars, and more – prior to critical junctures such as concrete pours and wall closures.
The review control findings are stored in a collaborative environment in a single source of truth and ultimately, construction teams can create and retain a full 3D history of jobsite progress and quality.
For example, in a concrete foundation plan spanning a few hectometers of space, a 2D reality map is created from a combination of images taken with a drone and a walking 360-degree video capture. The user can then directly overlay the 2D foundation drawing with the reality map and verify critical path foundation work. At this scale, the user can eliminate site access issues and walking time on site with a single capture that all team members can review, analyze, and perform quality control relevant to them.
The applications of quality control are manifold. Two examples are the Skanska City Gate and a Rebar Deck. In the Skanska City Gate project, the overlay of the BIM-model was used firstly to verify that the wall openings are in the right place according to the design of the heating, ventilation, and air conditioning (HVAC), and secondly to assure the production plan for the HVAC. The Citygate team used remote quality monitoring on a weekly basis - reviewing the work put in place and the planning work in a collaborative manner.
At the Rebar Deck project, drone and phone video capture produced a 3D model. A pre-pour quality review by a remote Project Engineer revealed that several concrete sleeves had been misplaced. This catch saved significant concrete rework that would have cost over $20,000 and several day’s slippage in the schedule. This quality control process is now used before every concrete deck pour. Overlaying the BIM model with the reality captured pre-pour catches mistakes that would become costly rework, even involving concrete drilling.
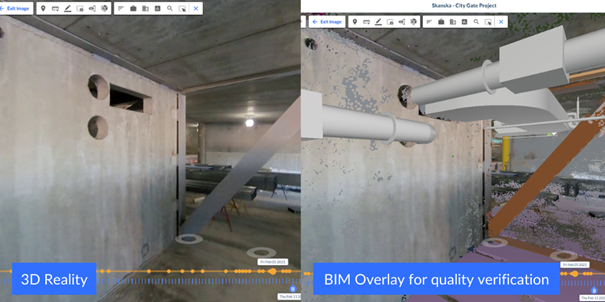
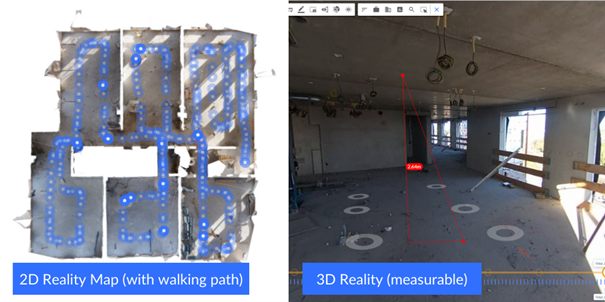
sample title for the image
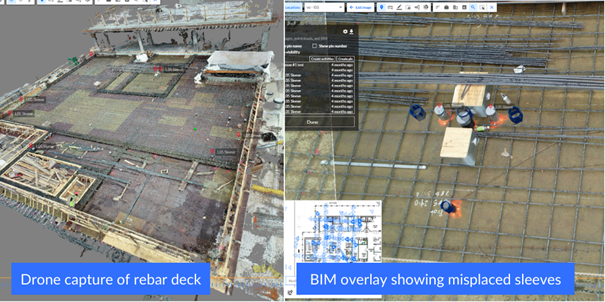
sample title for the image
Recurring Value of Remote Quality Control
Implementing reality mapping technology and enabling remote quality control can consistently deliver value to construction projects. Firstly, is enables the teams to verify quality that affects the critical path. Whether it is foundation layout, pre-concrete placement, or installing HVAC, having remote project experts confirming quality reduces rework on every project. Secondly, it can save on travel costs and workers on-site. Simply put, remote workers and stakeholders can now have an equal understanding of project progress and quality of work put in place compared to design and plan. And lastly, quality control can retain progress and quality history. After routinely capturing the site throughout the project, you will have a fully transparent record of progress and quality control throughout the project. This provides an excellent handoff to the owner and operator for the future life of the structure.
Remote quality control is a powerful tool to increase productivity and eliminate reworks due to errors and/or miscommunication. This does not only lead to a more efficient construction process and a more efficient construction industry, but also to less materials wasted – an important side-effect in times of material shortage, supply bottlenecks and climate crisis.
About Reconstruct Inc.
Reconstruct is a SaaS platform that utilizes images and videos from 360 cameras, drones, and cell phones to produce 3D reality models and automatically aligns these models over a project’s timeline. Reconstruct also allows BIM and project schedules to be integrated and automatically overlays the resulting 4D BIM against reality.
For construction projects, the resulting 4D digital twins highlight differences between as-planned and as-built conditions so that construction project teams can review construction quality, progress, and schedule risk to keep their projects on-schedule and on-budget.
The Nemetschek Group participated in the series B financing round of Reconstruct, Inc. in 2021.